Air-conditioning Systems for a Plastic Container Manufacturing Plant
Case study in the air-conditioning systems business area
Customer’s Issue
Need to develop a near-cleanroom-standard environment with an appropriate air-conditioning system for plastic container production lines
Business category:manufacturing / Employees:2,500 / Established:more than 100 years
Solution and Outcome
Developing production lines designed for high-quality products through air filtering, room pressure control and temperature management
Integrated control from the air-conditioners to air filtering, room pressures and humidity
We had a commission by a major packaging manufacturer concerning their project to launch new plastic container production lines, and our task was to provide an air-conditioning system for them. The purpose of this system was, first and foremost, to control the in-plant temperatures to enhance the production lines’ productivity, and also to provide the air-conditioning for their employees by maintaining comfortable environments. Requirements such as these often involve a coordination of air-conditioning with air filtering, room pressure control and humidity management. The plastic container production lines to be introduced represented a typical case of those factors to be taken into account.
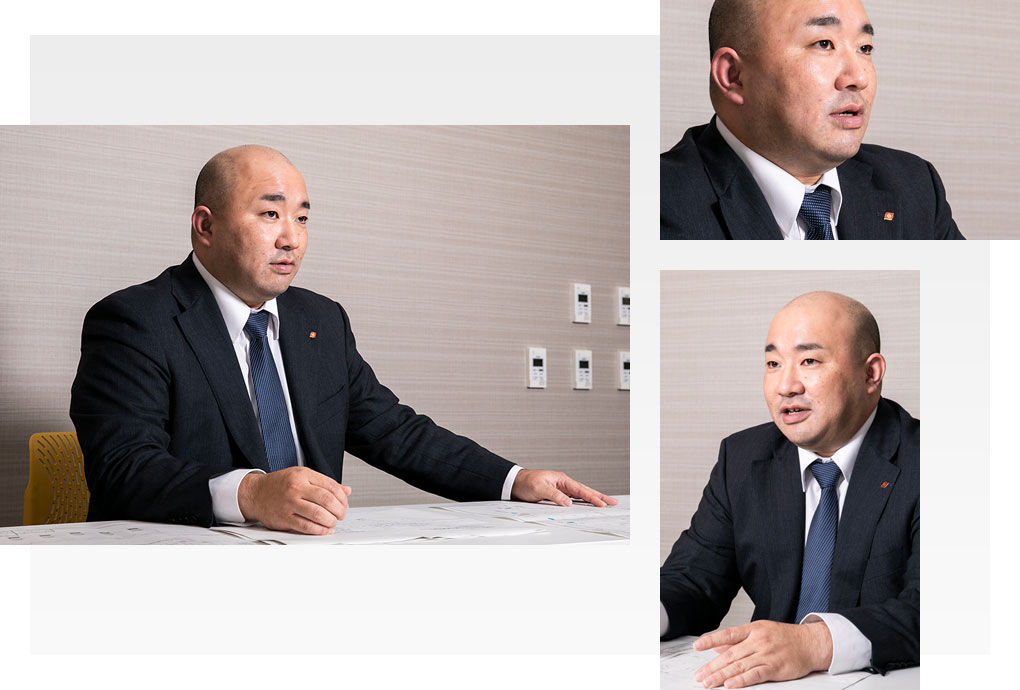
Designing the ideal environment through close communication with the customer
Blow molding machines for plastic containers use electric heaters to melt the raw material, thereby generating considerable heat. We started by reviewing their machines in terms of the levels of heat generation and associated air-conditioning loads required of the air supply and ventilation system. Based on the review, we selected an air cooled chiller (the equipment to create cooling water) as the appropriate cold energy source, then determined the details such as specifications and number of units required. This process also involved drawing up the piping plans both for the mains and for the machines.
The next point of consideration was the air filtering arrangement. The production lines had to be constructed to near-cleanroom standards, which meant blocking the inflow of the external air and ensuring positive room pressure (i.e., maintaining the air pressure in the room higher than the ambient pressure) to prevent airborne and insect contaminations. By contrast, the dry room placed immediately before the production lines, designed to feed the raw material plastic (in powder form), had to be a negative-pressure room to prevent the particles of plastics from contaminating the line space. This arrangement proved to be challenging in terms of maintaining the room pressure differentials.
Furthermore, temperature and humidity management had to be considered for spacious warehouses and storage areas for ensuring reliable product quality control. Japan has a pre-summer rainy season, when the ambient humidity tends to remain very high. For this reason, it was particularly difficult to work out the best arrangement and specifications for the air-conditioning and dehumidifying equipment. In the end, we managed to offer a good plan through close communication with the customer.
Our strengths in the know-how that enables us to understand the equipment and formulate an ideal air-conditioning system arrangement
The newly established plastic container production lines have been in operation without a glitch, and we had positive feedback from the customer. In fact, the client approached us as their first choice for the work. There are several vendors who specialize in updating industrial air-conditioning systems, but our competitors would be unable to handle the task of furnishing an air-conditioning system for an entire production line. The strengths in our approach to business are that we work closely with our customers, which allows us to have in-depth knowledge of their facilities and equipment.
For example, the air cooled chiller could be downgraded to lower the investment cost, but an arrangement with a minimum capacity would run a risk of grinding the business operation to a halt if, in the future, the chiller broke down. We took into account the maintenance and repair contingencies when designing the system, being mindful of the importance of keeping the production lines going and minimizing the operational risks for the customer. These points are part of the know-how that enables us to formulate an air-conditioning system arrangement that is ideal for customers, and this is our strength. Today, many businesses work hard on sustainability and SDGs, and we continue to strive to help them achieve their goals.
Contact Us
For detailed information about our products and services, please contact us using our inquiry form.